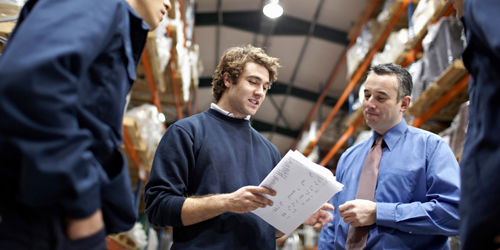
There's no doubt that managing a warehouse is an expensive job. When you start to add the cost of fixing mistakes, making up for lost time, and doing damage control, that expense shoots up.
The key to bringing costs down is, of course, a well-managed warehouse. When operations are running smoothly and systems are optimized, you can expect the highest profits along with a better, happier environment within the warehouse. That all starts with identifying where you might be going wrong.
Whether you're in charge of one or manage multiple warehouses, discover how to spot when things aren't optimized and how to fix them in this guide.
Unintentional Redundancies
In a warehouse, every product needs a set number of interactions with employees. These interactions are usually part of a larger system of operations, known as a workflow. When the workflow is running properly, the work is done efficiently and your products get where they need to be in the shortest amount of time. When redundancies start happening, that organized workflow is interrupted.
Redundancies occur when the same operation is carried out more than once, unnecessarily. For example, it's very frequent in order picking for more products that needed to be picked and moved. This wastes time during the operation, increases labour costs, and wastes further time when someone has to go back and correct the mistake, which is far from ideal.
One solution to this is tracking inventory, specifically barcode tracking. When an order is picked, a barcode is scanned and the inventory updated.
Having to Search for Equipment
In single or multi-warehouse management, organization is key. A huge sign that your warehouse is being mismanaged is if items aren't organized and staff are constantly having to spend time searching for what they need. This is a colossal waste of time and should be fixed as soon as the problem is noticed.
To make it easier, equipment should be easily tracked at all times. There should be specific spots for each piece of equipment that are known to all staff, and tracking will encourage staff to return the equipment when they're finished with it. This also prevents hoarding of equipment so that a member of staff has what they need all day even when not in use, which is a big problem in mismanaged warehouses.
Poor Warehouse Layouts
Efficient use of space is vital for a well functioning warehouse. If your space isn't well-designed, it's going to be much easier for equipment to be lost, products to be misplaced, and for operations to take longer than they should. For example, if you don't have enough storage items are going to be easily lost and time will frequently be wasted trying to find misplaced products.
An efficient layout makes use of floor space as well as the vertical space available. However, warehouses frequently fall short at maximizing the space available, with only around 68% of a warehouses capacity being used on average. Consider your layouts carefully to work out whether they're being used to their full potential.
There should also be easy accessibility to every area of the warehouse, and room to manoeuvre your equipment throughout. Bringing in equipment to maximize your space, such as forklifts, is another idea that should be considered.
Accessibility to items that are needed more frequently is a must. For example, the highest selling items should be placed in the most accessible areas. If you're struggling to optimize your space, look into warehouse management systems that can help.
Not Managing Inventory Properly
Inventory mismanagement is one of the most common problems in warehouses. It can lead to a variety of problems, including:
- Products placed in the wrong areas
- Accepting orders that can't be fulfilled (leading to backorders and extended lead times)
- Denying orders you think can't be fulfilled only to find that they can be
- Struggling to store new stock
These issues can easily happen when there's either no inventory recording system in place, or it's being done manually. An easy solution is to use customizable inventory software that tracks your inventory for you, reducing the chance of human error. These real-time systems collect data through devices like barcode scanners, which tracks your goods with ease so you know exactly what you have in stock at any given time.
The best inventory management software is reliable, easy to use, and offers advanced customizable features.
Forgetting the Accounts
A lot of managers overlook the fact that accounts and warehouse management are closely linked. Your profits, losses, and assets are all based on what comes in and out of your warehouse, and if you don't have your accounts in order, the warehouse is going to be incredibly difficult to manage. For example, for smaller businesses, you may accept an order for products that you currently don't have the funds to produce.
These events are rare, but they do happen for small companies and startups. To avoid them, use full financial accounting software that links to your inventory, automating your systems with ease.
Manage Multiple Warehouses Without Compromising on Efficiency
If you have to manage multiple warehouses or even just a single warehouse, you need to remember that organization is key. When your system is organized, you reduce human error, save time, and create a more profitable system.
If you're interested in upgrading your warehouse with inventory software, be sure to check out the platforms we have at Liono360. To find out more and see how they could help transform your operations,